Home » Posts tagged 'printing'
Tag Archives: printing
Understanding the Cost Structure of 3D Printing
3D Printing Arizona is a fabrication process that produces three-dimensional objects layer by layer. This technology is a viable alternative to traditional manufacturing methods.
First, a virtual design of the object is made using computer-aided design (CAD) software. This model is then translated into machine instructions that tell the printer where to solidify each material layer.
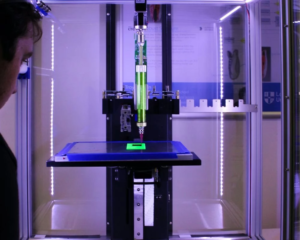
3D printing is a great solution for increasing productivity in your manufacturing process. But, it’s important to understand its cost structure before implementing it. This will help you to determine whether it’s right for your business or not. 3D printers vary in price, from basic desktop models for hobbyists to industrial-grade machines that can cost thousands or tens of thousands of dollars. The size, complexity, energy consumption, and maintenance costs of your printer will all influence its overall cost. You’ll also need to consider the type of materials used, which can be expensive or affordable depending on your needs.
The first step in the process is to create a virtual model of your product using computer-aided design (CAD) software, which works like a blueprint for the printer. Then, the model is sliced into many layers using a process called “slicing.” This allows the 3D printer to build your part one layer at a time. This makes the process more efficient and affordable, as the print times are much shorter than with traditional methods.
Fused deposition modeling (FDM) is the most economical 3D printing technology for prototyping and low-volume production. The process uses UV-cured photopolymers to create a solid object from thin layers. Its speed, versatility, and material choices make it a great choice for rapid prototyping and the manufacturing of small parts.
While the technology is still new, it has become increasingly popular for manufacturing applications. For example, it can be used to create bespoke, made-to-measure medical devices, such as hearing aids and hip replacements. The rail industry has also embraced the technology, using it to make customised parts such as arm rests for drivers and housing covers for train couplings.
Another key advantage of 3D printing is its ability to eliminate the need for costly tooling and setup costs. While DFM analysis can reduce these costs, they can still add up to a significant amount of money up front. By contrast, 3D printing is a completely digital process that enables on-demand, agile production. It also supports more design freedom, allowing manufacturers to create complex geometries that can improve performance and aesthetics.
Speed
3D printing is a manufacturing process that builds up objects sequentially rather than casting or molding them as a single step (a consolidation process) or cutting and machining them from a solid block of material (a subtractive process). This allows for greater productivity, especially when compared to traditional fabrication methods. It also eliminates the need for complex tooling and other expensive infrastructure, which can be costly and time-consuming.
The speed of 3D printing depends on several factors, including the number of layers printed per minute, the print bed size and the thickness of each layer. In addition, the printer’s travel speed determines how fast it can build up a print without sacrificing quality. A faster travel speed enables the printer to complete a part in less time and decreases the risk of mechanical failure.
Another factor that influences the speed of 3D printing is the infill pattern, which determines how much material is used to support the outer shell of a print. A higher infill density creates stronger prints, but it also requires a longer print time. To increase the print speed, manufacturers can choose a more straightforward infill pattern, such as grids or lines.
In addition, the build direction and the volume of the support structure can also affect the print speed. In order to increase print speed, engineers can minimize the build direction and the number of layers deposited per minute. They can also reduce the build height and orient the model to minimize the need for support structures.
Having an in-house 3D printer can boost a company’s productivity by allowing them to develop products and prototypes quickly, which is crucial for resiliency. It also reduces reliance on outsourced providers, which can be vulnerable to supply chain disruptions and other operational challenges. As such, it can help businesses move from CAD to print in 80-90% less time than traditional fabrication methods, which is particularly important for small batch production or short-term projects. In addition, 3D printers can also help businesses consolidate parts into a single design and reduce the need for assembly, which improves overall production efficiency.
Durability
A key factor in a 3D printed object’s durability is the material that it is made from. Durable printers typically use industrial-grade filaments and resins that are known for their durability, such as PEEK or ULTEM. These materials require higher heating temperatures than standard filaments, so it’s important to choose a printer that can accommodate them. Otherwise, the prints may not be strong enough to withstand the stresses of an industrial environment.
To create a durable print, engineers first make a virtual design of the object using computer-aided design software (CAD). This process is similar to creating a blueprint for a physical structure. Then, the model is broken down into layers that will be solidified by the printer. The layers are arranged in a horizontal plane, and the printer builds up the object layer by layer, using its own internal instructions. Once the layers are complete, the printer uses a UV light to cure the object.
Once the printed part is finished, it can be tested for strength and durability by performing a variety of tests. Some of these tests include tensile, compression, and impact testing. Tensile testing measures how much stress a part can endure before it breaks. Compression testing reveals how well a part can resist compressive forces. And impact testing determines how much energy a part can absorb before breaking, which is useful for designing parts that will experience shock or vibration.
These tests can help engineers ensure that their designs will withstand the demands of their intended applications. For example, NASA used 3D printing to fabricate components for its rocket engines that must withstand extreme heat and pressure. By separating the combustion chamber liner and nickel super-alloy jacket into separate pieces, NASA was able to build a stronger engine that could handle extreme temperatures and pressures.
Additionally, 3D printing can increase productivity by reducing the time it takes to prototype new products and devices. In some cases, this can reduce production costs by up to 80-90% compared to traditional manufacturing methods. It also allows businesses to respond quickly to changes in demand by easily increasing production capacity by adding more printers. This can help companies avoid expensive retooling and storage costs that are associated with traditional manufacturing processes.
Sustainability
3D printing has a number of potential advantages over traditional manufacturing processes. It can be faster, cheaper and more environmentally friendly. In addition to its benefits, it also allows manufacturers to customize products and create unique designs that can’t be easily made using other methods. It can be used to make parts for a wide range of industries, including aerospace, healthcare and automotive.
To print an object, the first step is to make a virtual design of the object. This can be done using a computer-aided design (CAD) program or by scanning an existing object. Then, the model is sliced into hundreds or thousands of layers for printing. This process reduces material waste by printing only the necessary portions of the model.
Most commonly, 3D printers use thermoplastic materials. These materials can be recycled to produce new filaments, which makes 3D printing an extremely sustainable technology. However, it is important to choose the right filament for your printer. The type of filament used is important because it affects the finished product’s strength and appearance.
The most common thermoplastics are PLA and ABS. Both of these materials are derived from renewable resources and can be recycled after use. But there are other filaments that can be used, such as PP and nylon. These materials are not as durable as ABS and PLA, but they have a lower melting point, so they can be printed at higher temperatures.
Another advantage of 3D printing is its ability to create parts that are lighter than those produced by conventional methods. This can help reduce shipping, inventory, and storage costs. It can also help companies improve efficiency by reducing the weight of their machines. For example, a company called Jabil has integrated 3D printing into its operations. This has reduced the amount of glue, packaging and time spent on assembly.
One of the main problems with traditional manufacturing is the massive carbon footprint created by transportation of raw materials. The energy used to transport these materials contributes significantly to climate change, and the use of 3D printing can substantially reduce this impact.